
L’impression 3D classique, fonctionnement et usages
L’impression 3D est un domaine vaste, regroupant plusieurs dizaines de techniques et d’appareils, et bien plus encore d’usages. Mais un principe simple est à la base de ce mode de production si prometteur : la fabrication additive. La fabrication additive consiste en une création couche par couche de l’objet final. Par exemple, si l’on décide d’imprimer une tasse de café, que ce soit par photopolymérisation ou par liage de couches, le principe restera le même : l’objet est décomposé en plusieurs tranches par le logiciel de Création Assistée par Ordinateur (CAO). Le fichier 3D est envoyé dans le microprocesseur de l’imprimante et la buse d’impression (ou laser en fonction de la technique utilisée), par dépôt de matière en fusion ou de poudre dessine le contour de l’objet selon un dessin plat spécifique. Ce contour est rempli, comme un enfant remplirait un coloriage. Lorsque la première couche est ainsi réalisée, la buse d’impression s’élève de quelques centièmes (ou millièmes) de millimètre, revient à son point de départ et répète le processus.
La succession de ces couches finit par former l’objet tridimensionnel dessiné par Création Assisté par Ordinateur.
C’est donc un processus de fabrication à l’opposé de méthodes plus traditionnelles comme le fraisage, le découpage, l’usinage, qui reposent sur la soustraction de matière pour aboutir à l’objet final.
Maquette de villa imprimée en 3D (crédits : Ducaroy Grange)
Cette maquette par exemple, n’aurait pas pu être réalisée par un moulage plastique classique. Il aurait été impossible de sculpter aussi finement les colonnes soutenant les balustrades, de représenter de minuscules détails en relief sur les murs… De plus, une fabrication traditionnelle aurait nécessité la création d’une petite chaîne de production, avec un moule spécifique, qui n’aurait été utilisée que pour ce projet.
Avec l’imprimante 3D, le même appareil peut produire des objets opposés du tout au tout, sans devoir apporter de modifications dans la chaîne.
Nous allons maintenant détailler deux des principales techniques d’impression 3D utilisées de nos jours.
Commençons avec la technique la plus courante, visant entre autres le grand public : l’impression par dépôt sélectif, ou Modélisation par Dépôt de Fil en Fusion, abrégé en anglais FDM.
Imprimante FDM destinée aux particuliers ou aux PME (https://www.3dnatives.com)
C’est une méthode qui peut être utilisée avec presque tous les matériaux ayant une température de fusion de l’ordre de 300°C ou moins, ou pour des matières comestibles comme le sucre ou de la pâte.
Son principe de fonctionnement est plutôt simple : après que le micrologiciel de l’imprimante aie lu et séquencé comme expliqué précédemment le fichier STL réalisé par CAO, la buse commence son déplacement. La tête va se déplacer selon les 3 axes x, y, et z pour réaliser l’objet en couche par couche. Sur certains modèles, la buse réalise un dessin plan, laissant le plateau se déplacer de manière verticale.
Pour une imprimante à filament ABS, le plastique est fondu par la pointe de la buse et est déposé sur son parcours.
Même si les imprimantes FDM permettent un choix de matériaux très éclectique, les objets obtenus par ce biais sont cependant relativement fragiles (des plastiques comme l’ABS ne peuvent pas être utilisés pour des pièces subissant de fortes contraintes, par exemple dans des domaines industriels de l’acabit de l’aéronautique).
Voilà pourquoi il existe une autre méthode assez proche de la FDM, appelée LENS, destinée à un usage industriel.
Continuons donc avec la Mise en Forme par Laser, appelée LENS (de l’anglais Laser Engineering Net Shaping).
La tête d’impression est pourvue de 3 ou 4 lasers, qui convergent en un seul point (le point focal). De la poudre métallique est projetée à travers le faisceau. Les quelques particules qui atteignent le point focal des lasers fondent et fusionnent instantanément. La tête d’impression se déplace selon le même principe qu’une imprimante à dépôt sélectif précédemment présentée.
Cette technique est destinée exclusivement à l’industrie, de par les risques encourus lors de son fonctionnement. Elle permet l’impression des matériaux à la température de fusion la plus élevée, comme l’acier, l’aluminium ou même le titane. On peut d’ailleurs imprimer des pièces faites d’alliages en projetant des poudres issues de différents métaux.
C’est avec la LENS que les industries aéronautiques et automobiles se sont intéressées à l’impression 3D, qui leur a permis la réalisation de pièces très spécifiques, comme des pales de turbine en titane pourvues d’un système de refroidissement interne construites d’un seul bloc.
L’imprimante 3D possède donc de nombreux avantages par rapport à des techniques classiques de fabrication
Elle est donc destinée à tous les domaines de l’industrie nécessitant la réalisation de formes complexes, d’objets montés d’une pièce sans assemblage, des pièces très spécifiques ou des objets personnalisés…
Voilà pourquoi la communauté scientifique commence à s’intéresser à une application médicale : une méthode de fabrication industrielle ultraprécise, permettant la production de n’importe quelle forme avec n’importe quel matériau sous de très courts délais revêt un grand intérêt pour des laboratoires pharmaceutiques qui voudraient tester des principes actifs directement sur les organes concernés en contrôlant tous les paramètres de l’expérience, ou plus directement pour les 20 000 patients en attente de greffe en 2016 qui pourraient bénéficier d’un organe sur-mesure.
Système EOS P396 (crédits: http://www.primante3d.com/)
Des chercheurs se concentrent depuis quelques années sur la réalisation d’une “encre biologique” pouvant être imprimée en 3D, voici les résultats auxquels ils sont arrivés jusqu’à aujourd’hui :

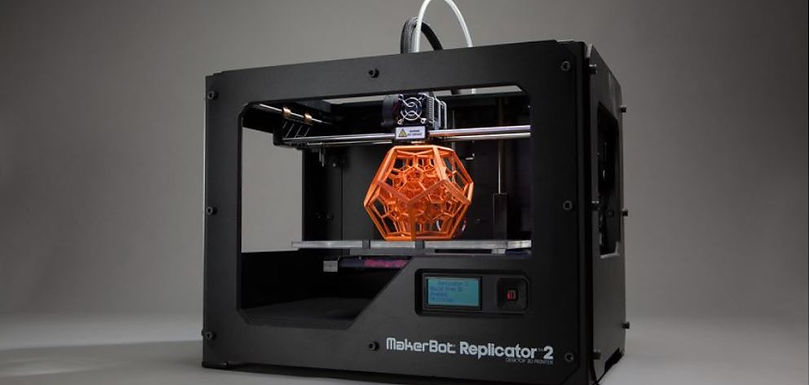
